Russian Ambassador's Residence

In this phase, our work was limited to third floor fenestration.

These large casement sash are replacements the Russians made in the ‘90s. Very unusual to see sash made of plain sawn oak in this region. They had fit problems and failing insulating glass.
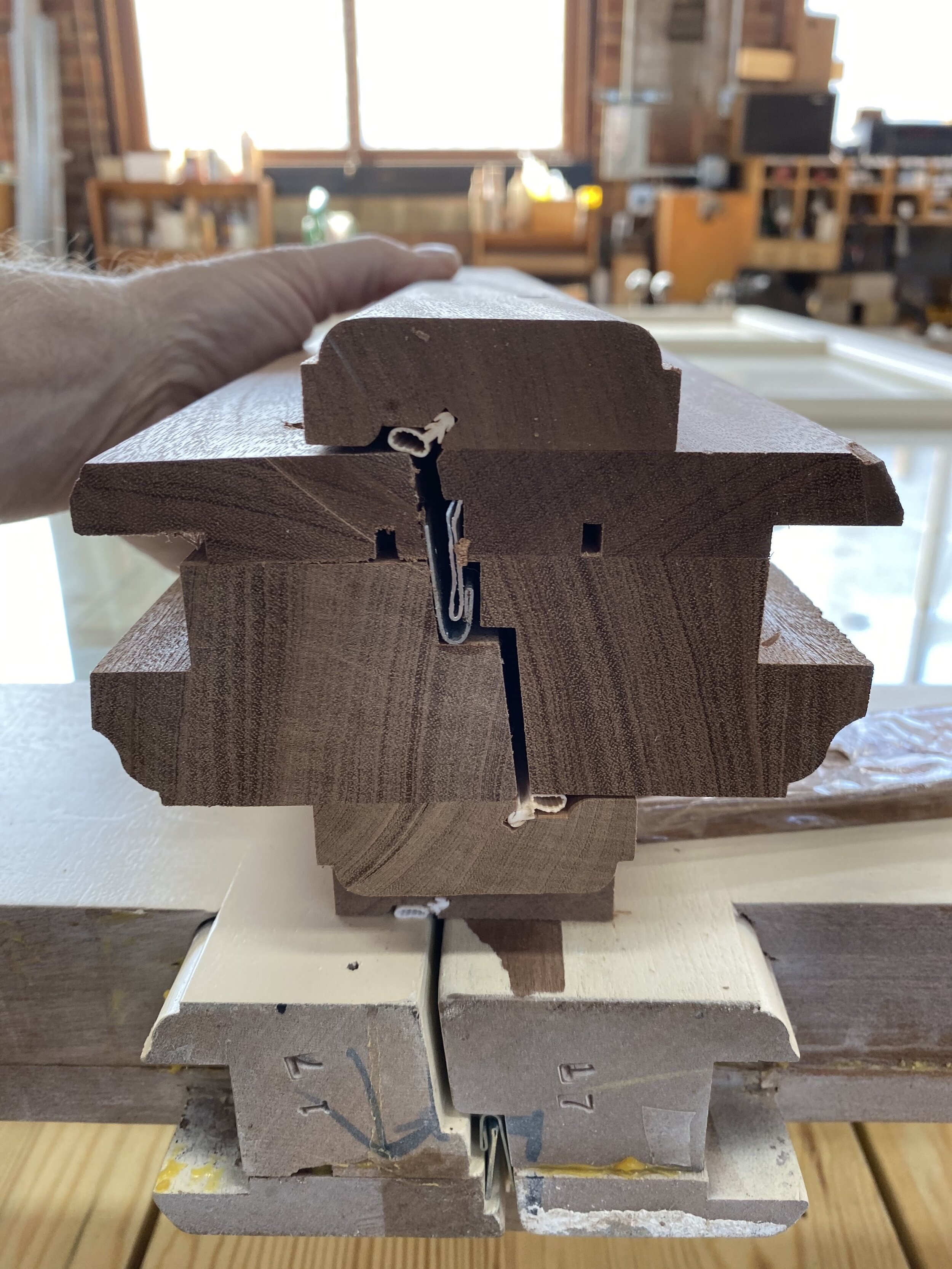
Early mock-up for enhanced meeting stile weatherstripping. Traditional interlocking zinc weatherstripping enhanced with modern silicone rubber bulbs. We added a third piece of silicone tube in the bend of the zinc metal at the center.
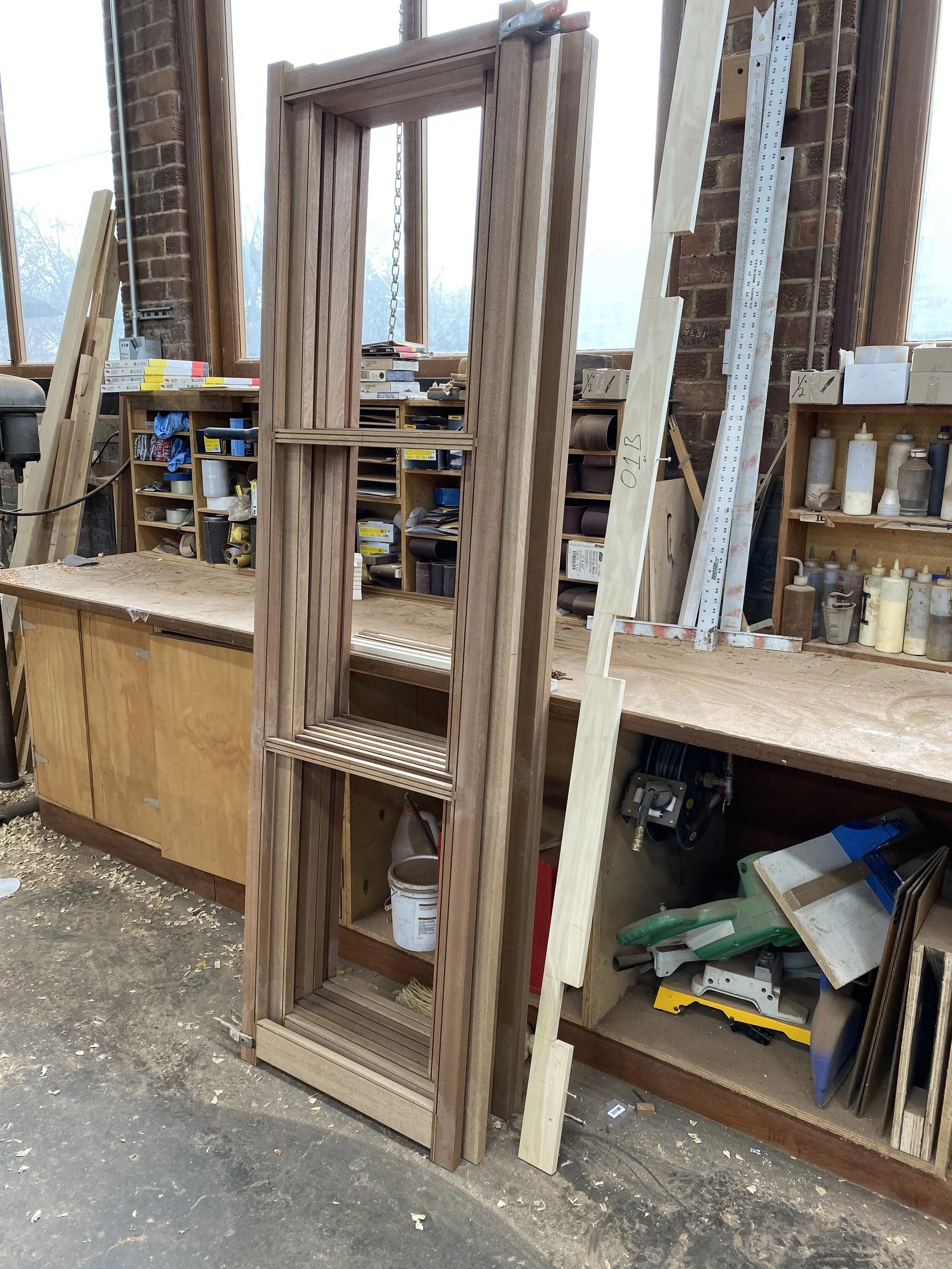
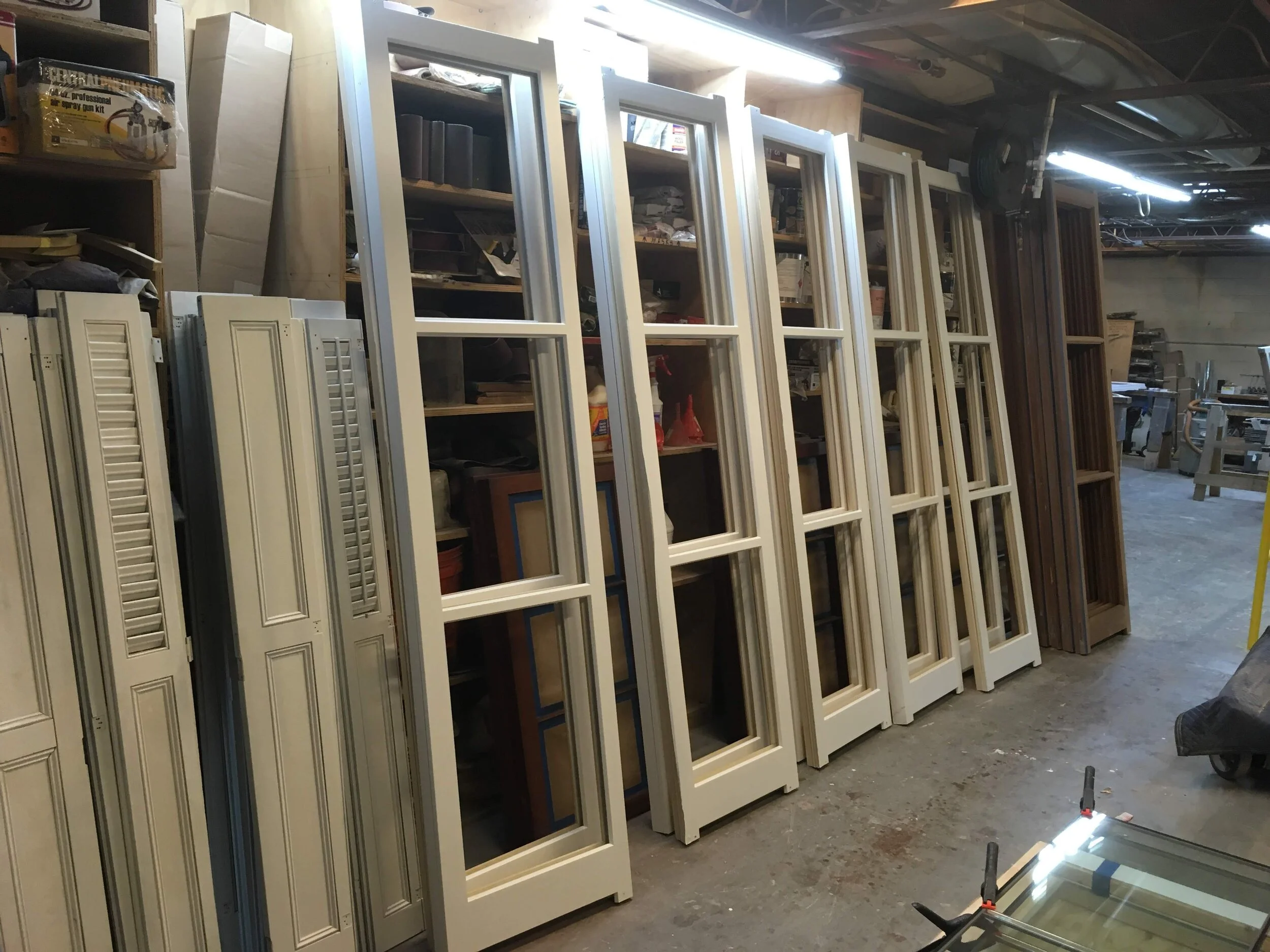
All finishing done in house, these sash received their acrylic paint in our spray booth.
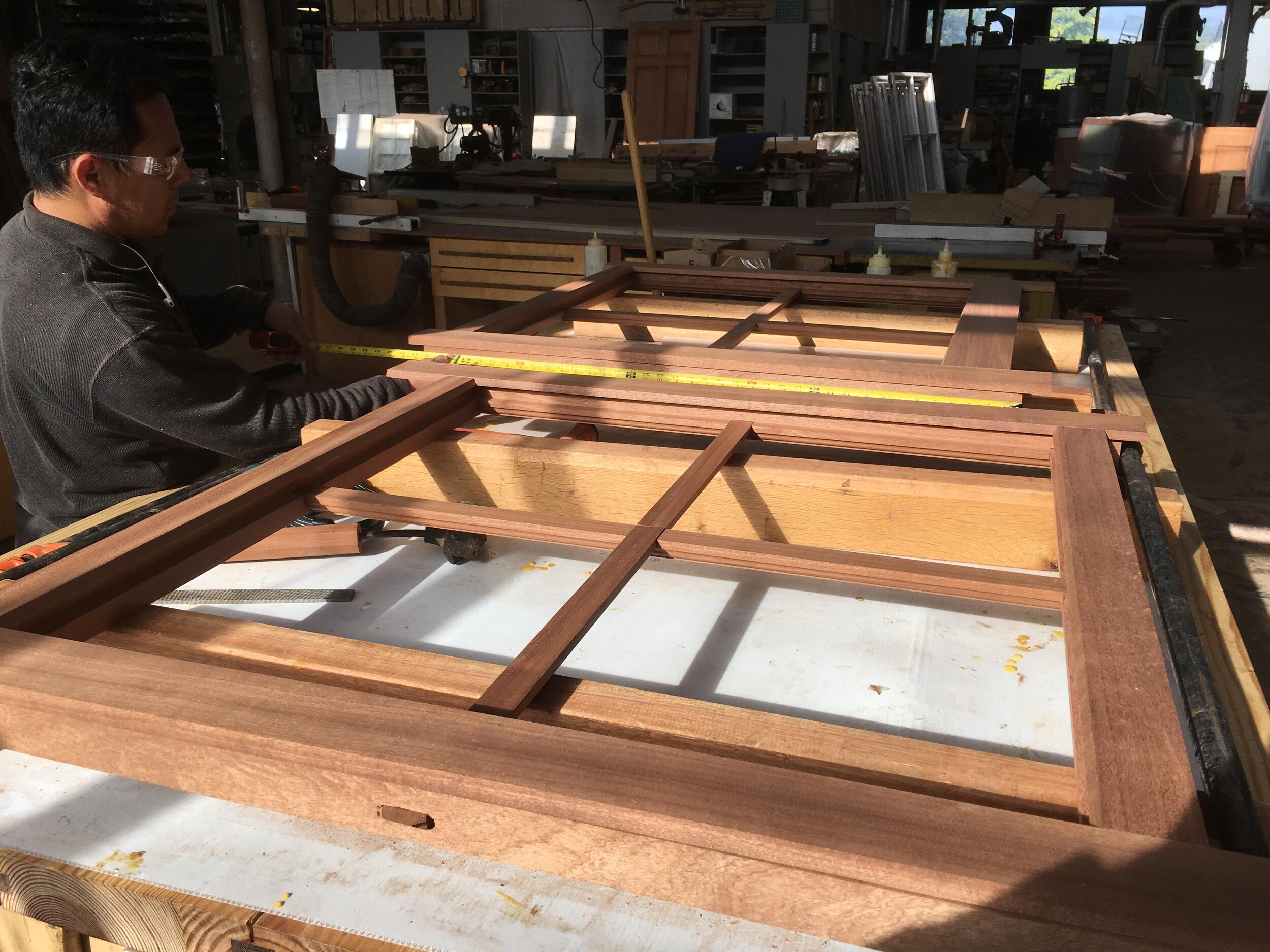
These are the few double hung sash we made using the same technique for the thick insulating glass. We made two sash frames for each opening.
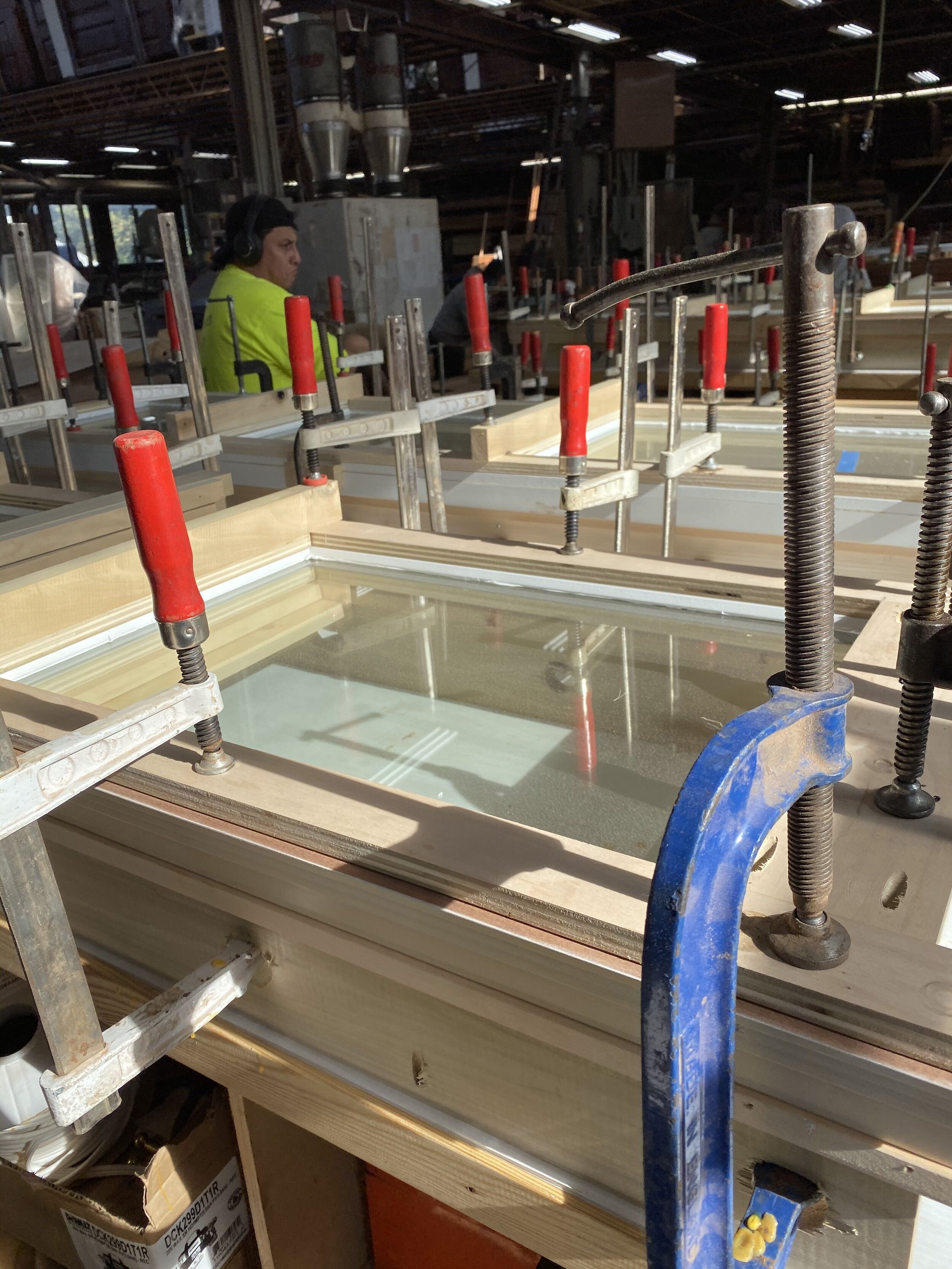
For a durable, seamless, and authentic profiles at the exterior, these thick sash were basically two components laminated together.
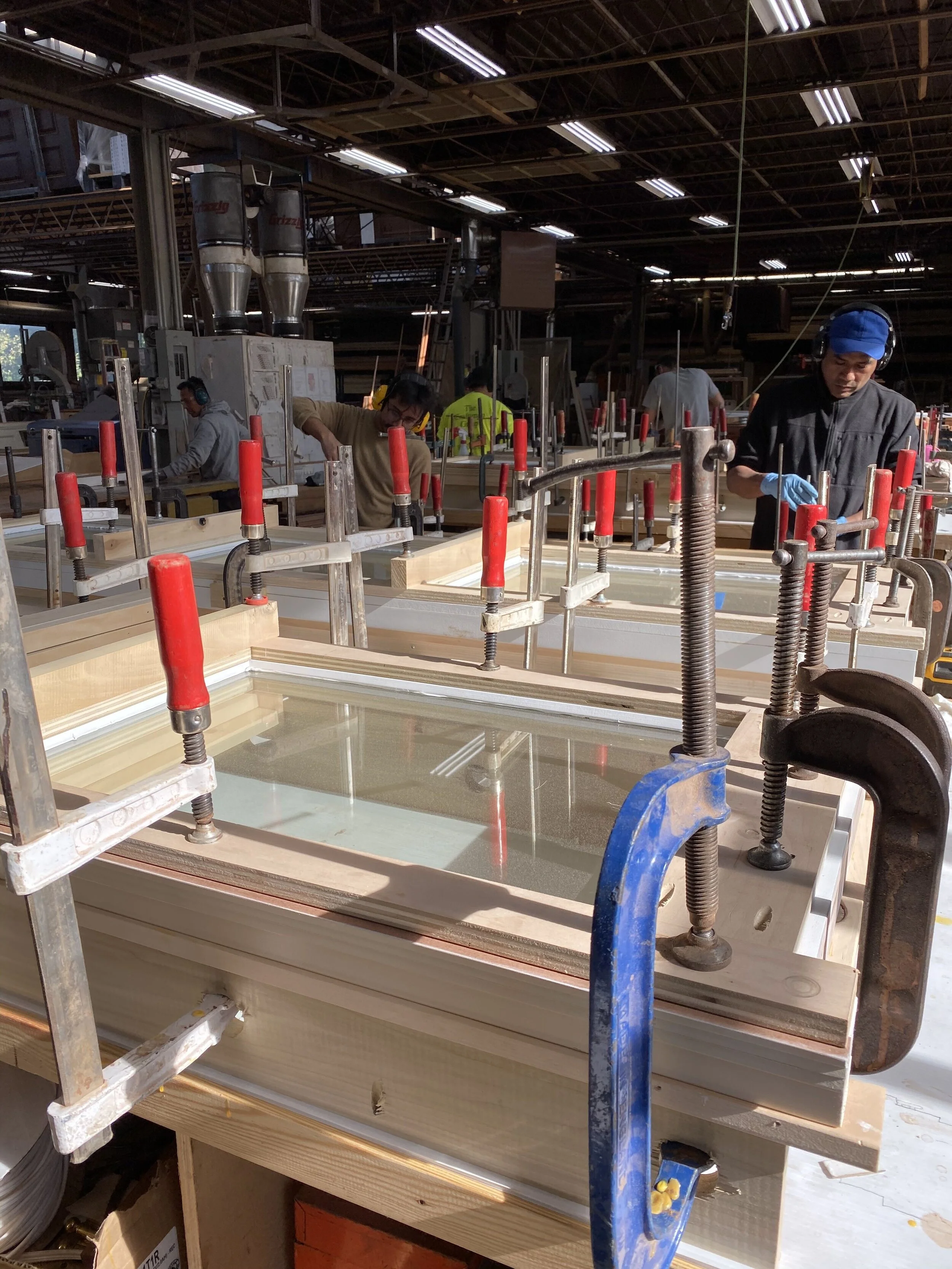
High performance polyurethane caulk is used at the joint between glass and wood.
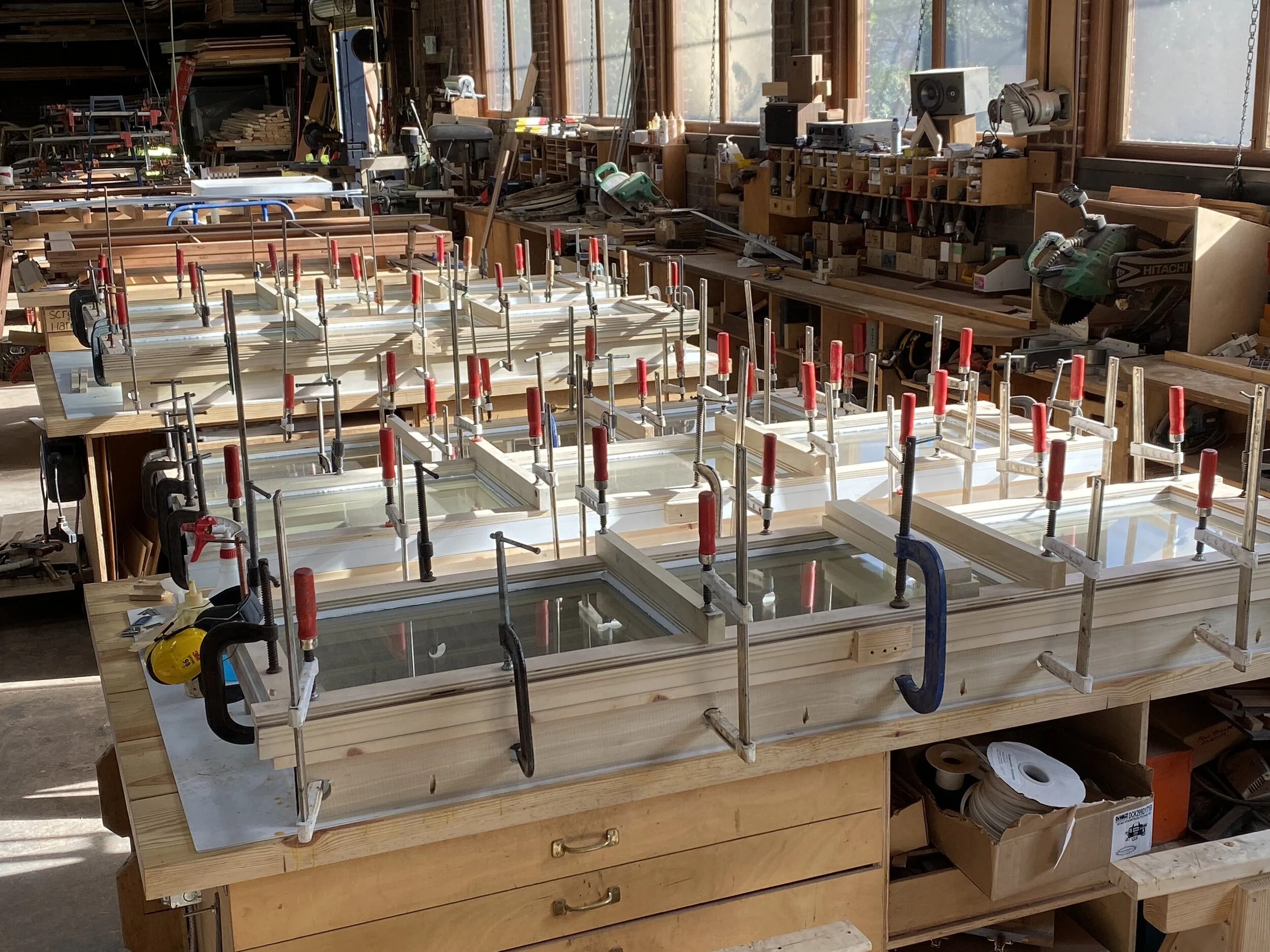
Clamping jigs kept sash dead flat.
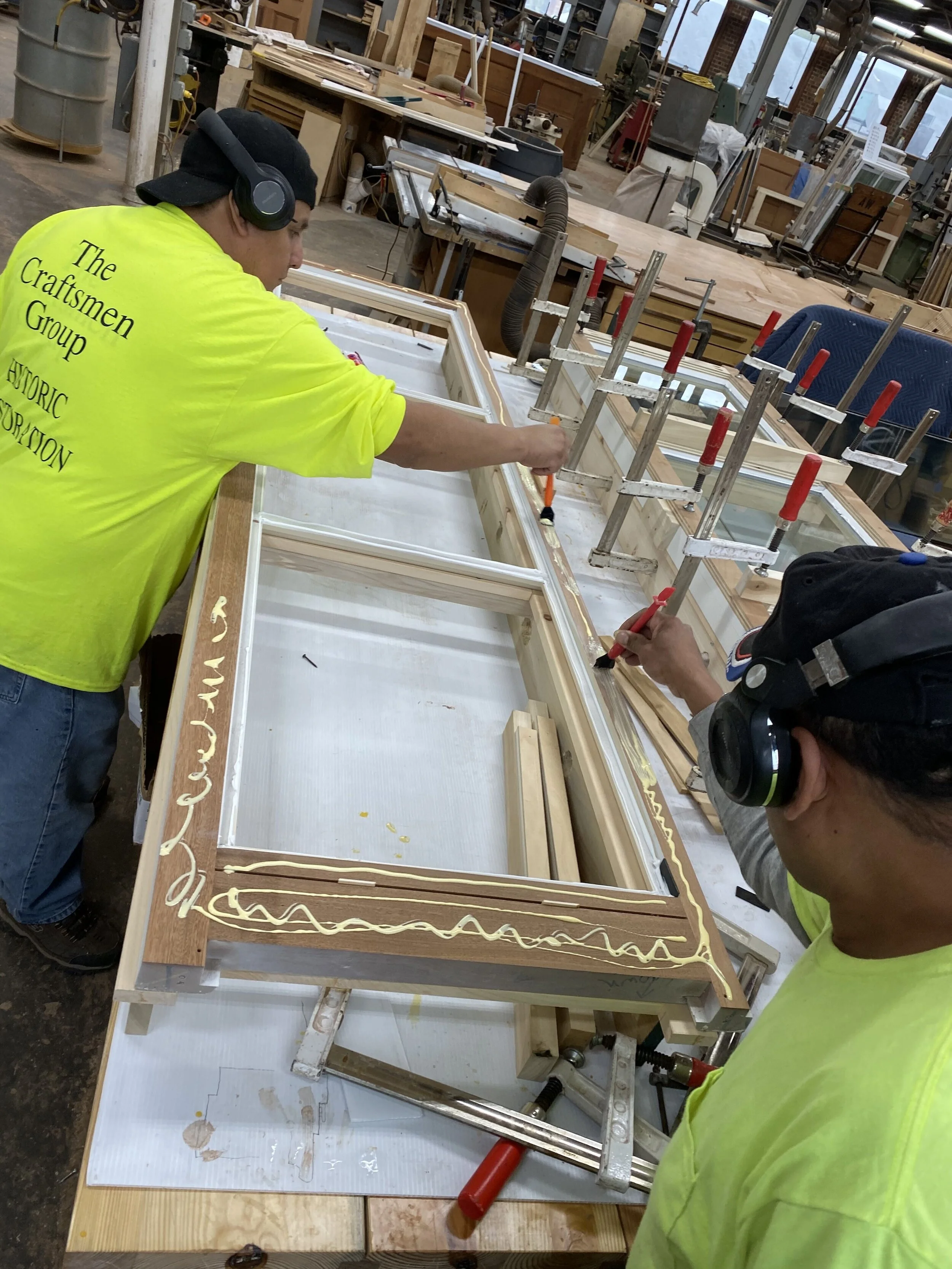
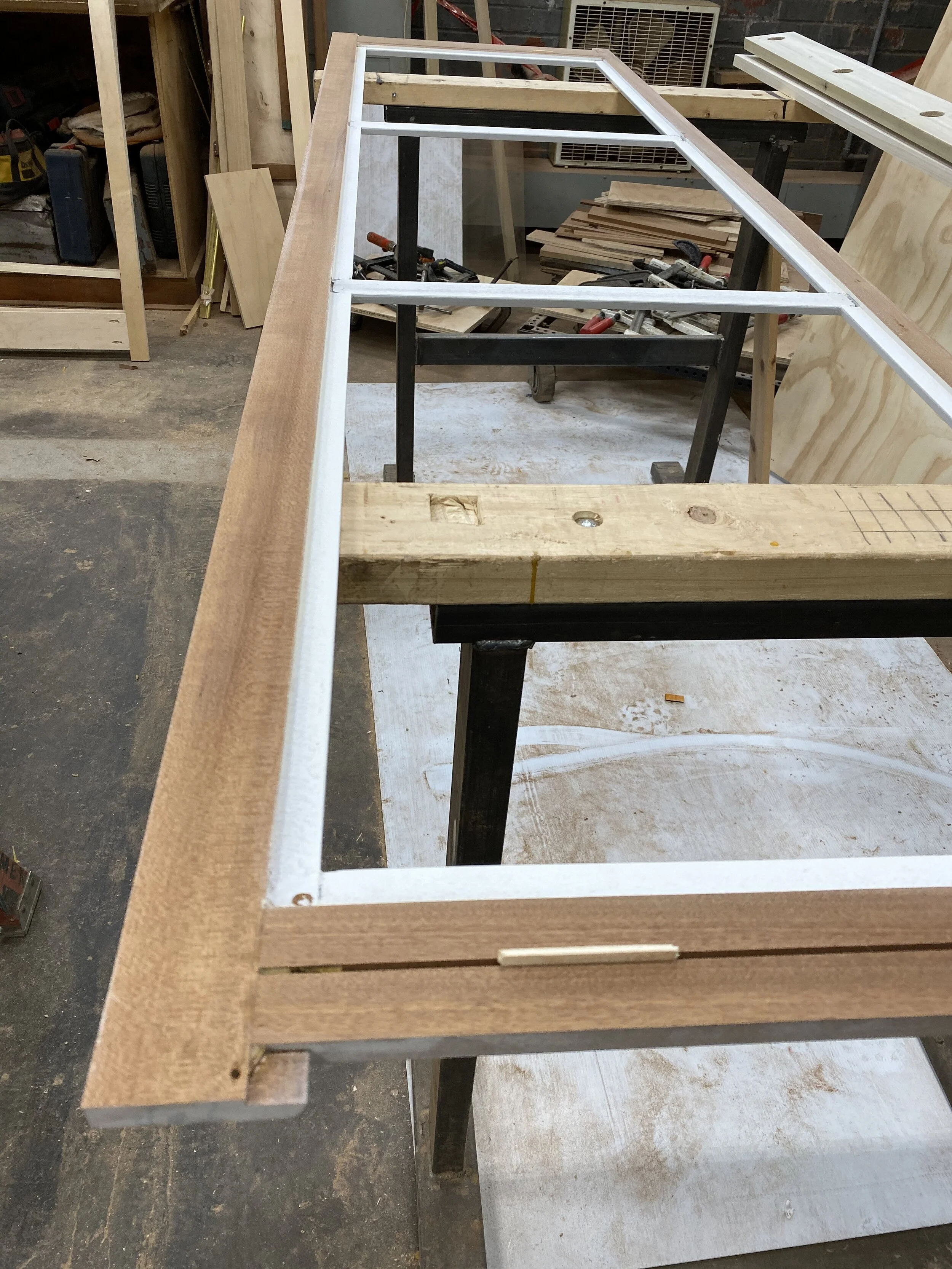
Note the groove in sash in foreground, this provides an index for perfect alignment between the two sash layers.
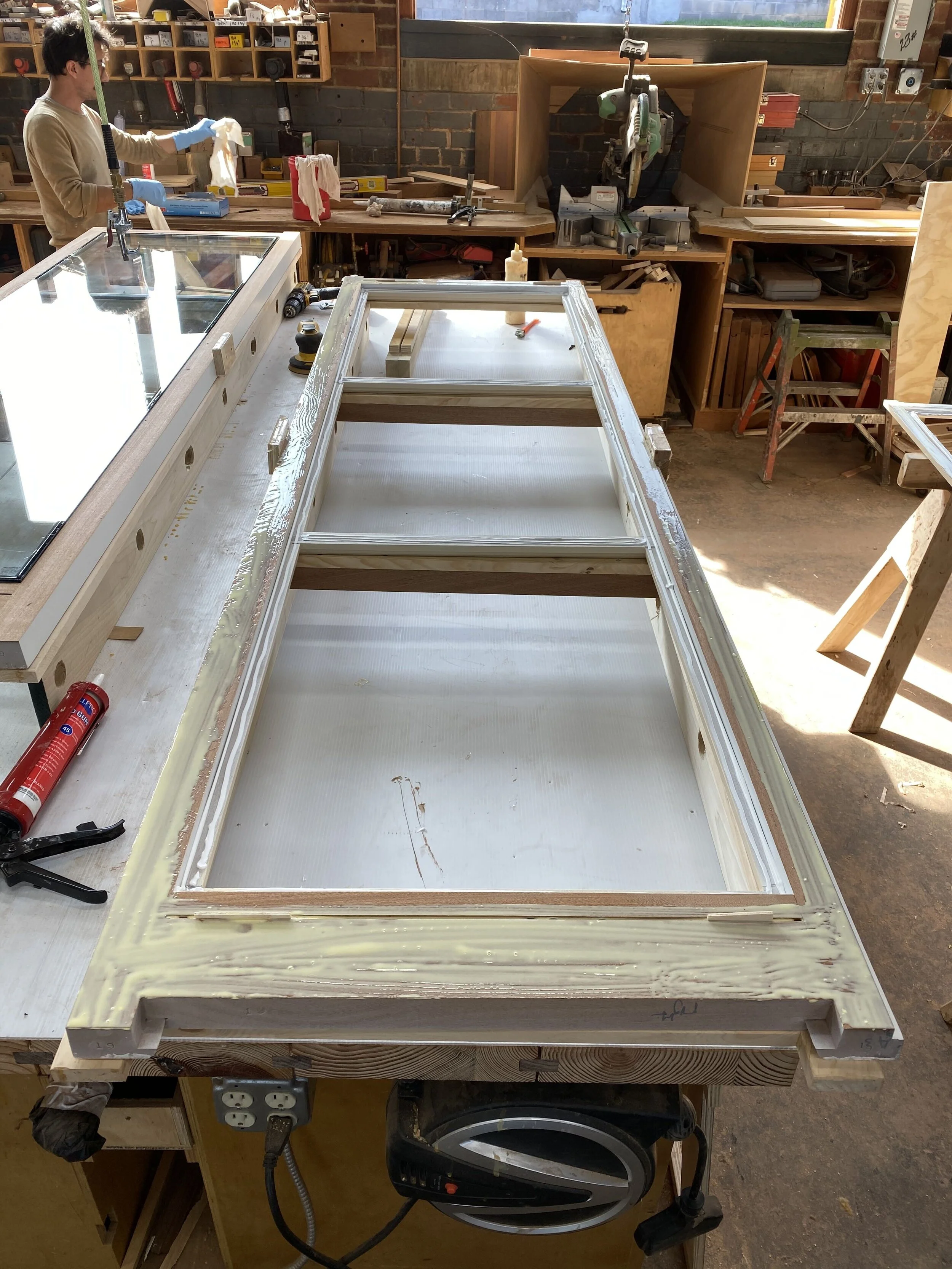
Fabricating the insulating glass panels in house allows us to coordinate the alignment of the three layered muntins perfectly.
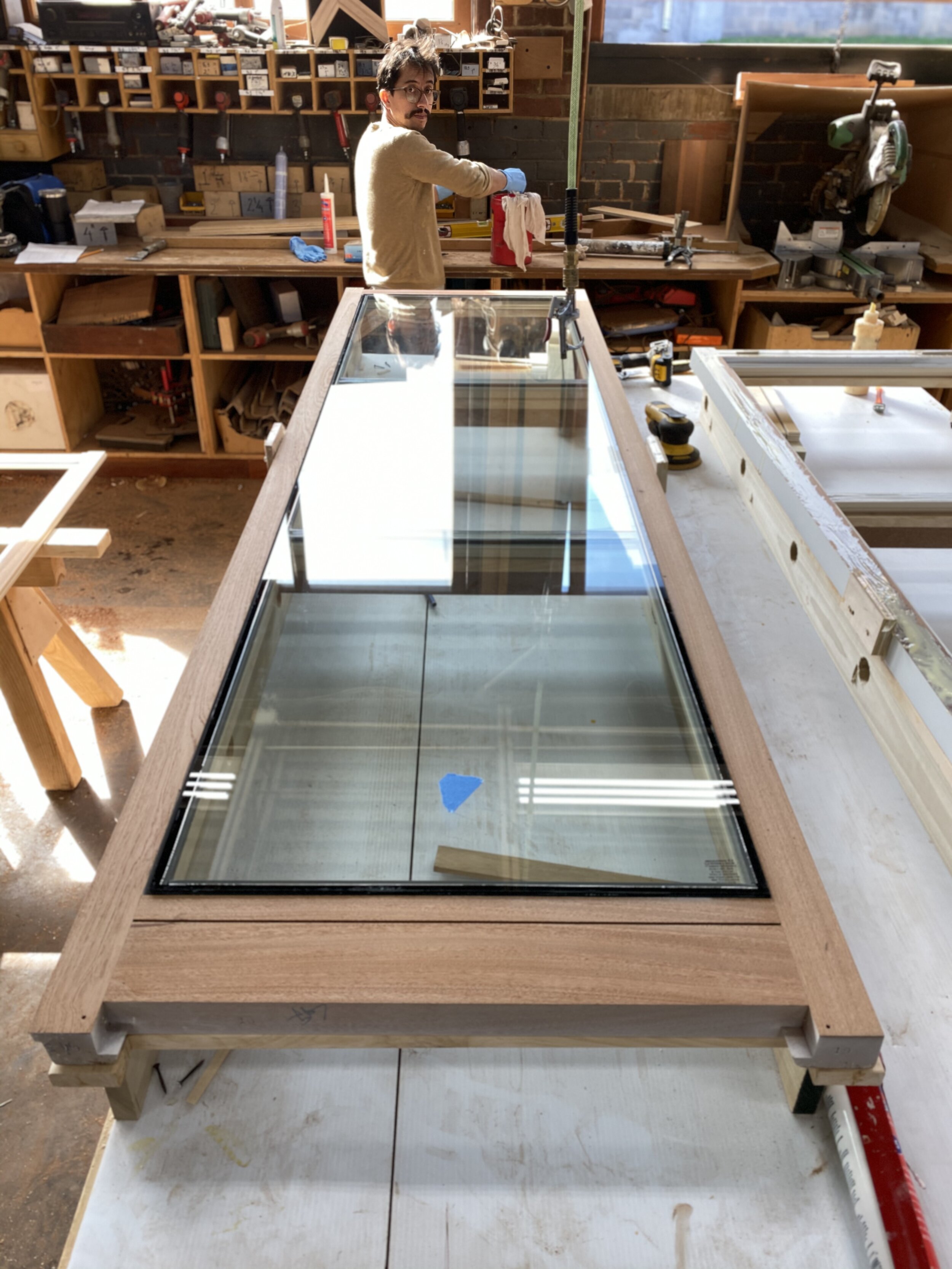
Further, we can provide more space for more sealant where it is most needed at the bottom of the sash.

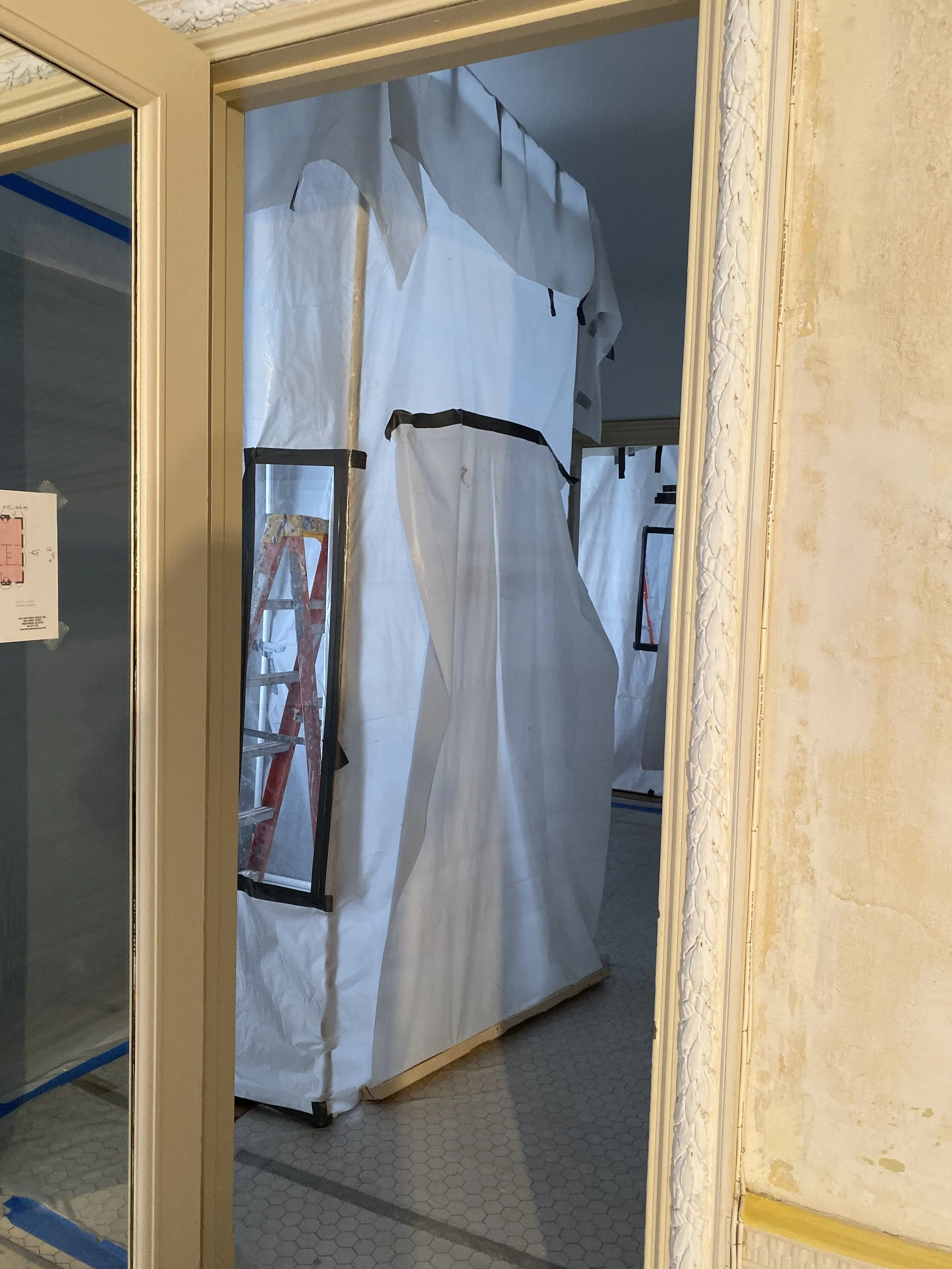
The Russians were cooperative and thoughtful in their communication, they did insist we install these viewing windows in thee containment chambers and maintain security in every room.
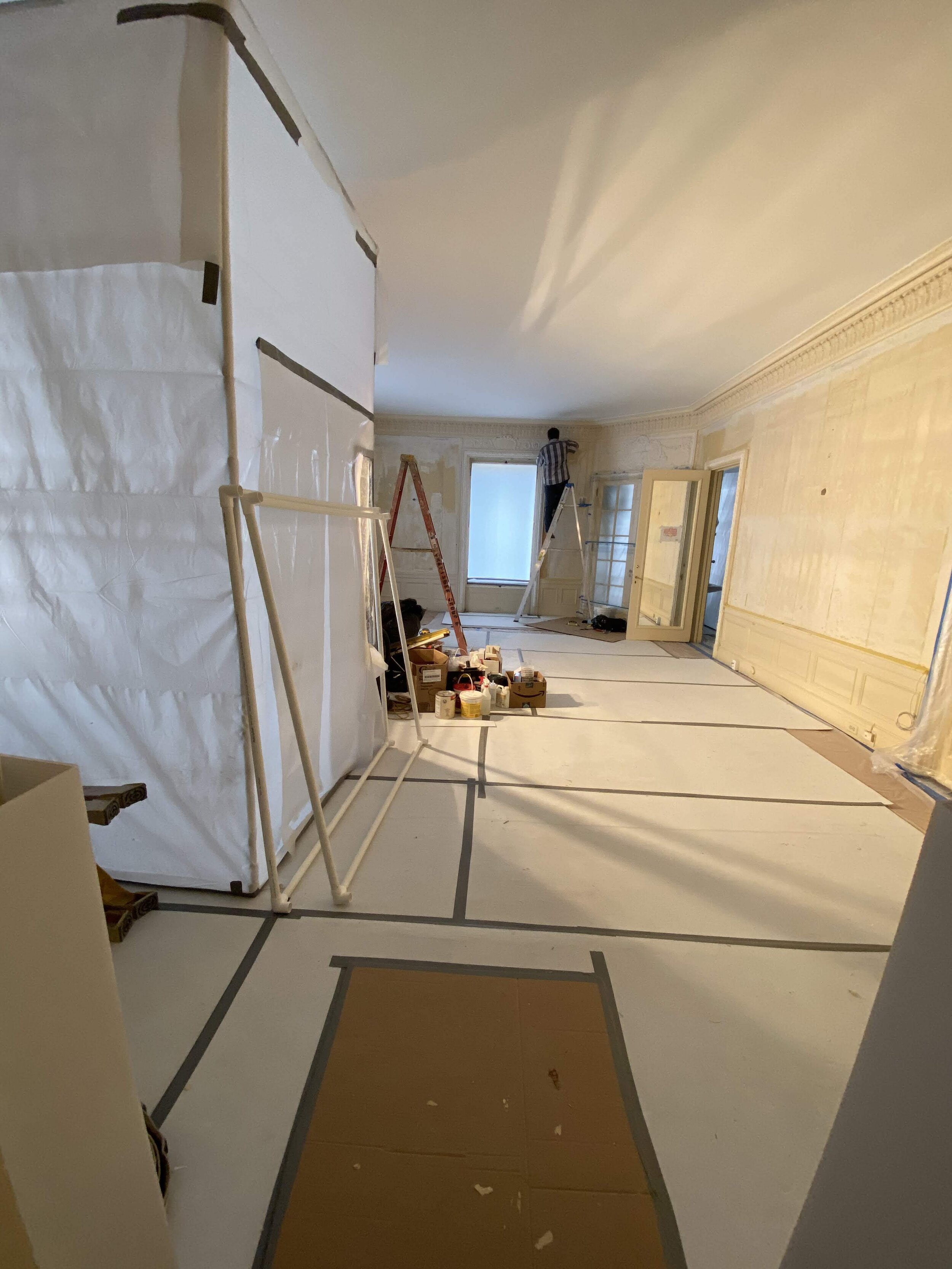
This is the ambassador’s home office. Protection and containment throughout the project were paramount.
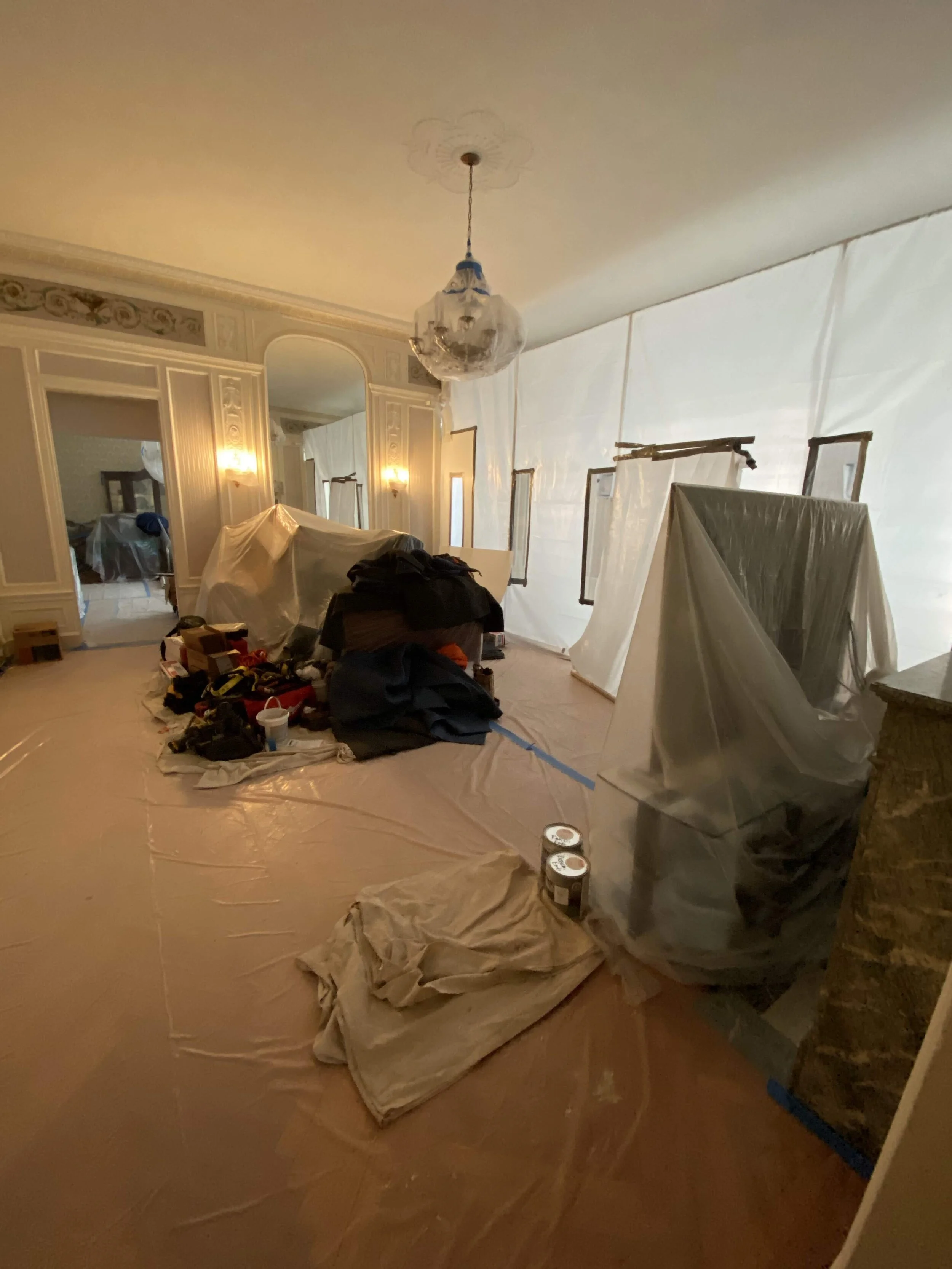
The ambassador moved out for two months during installation. This is his dining room.
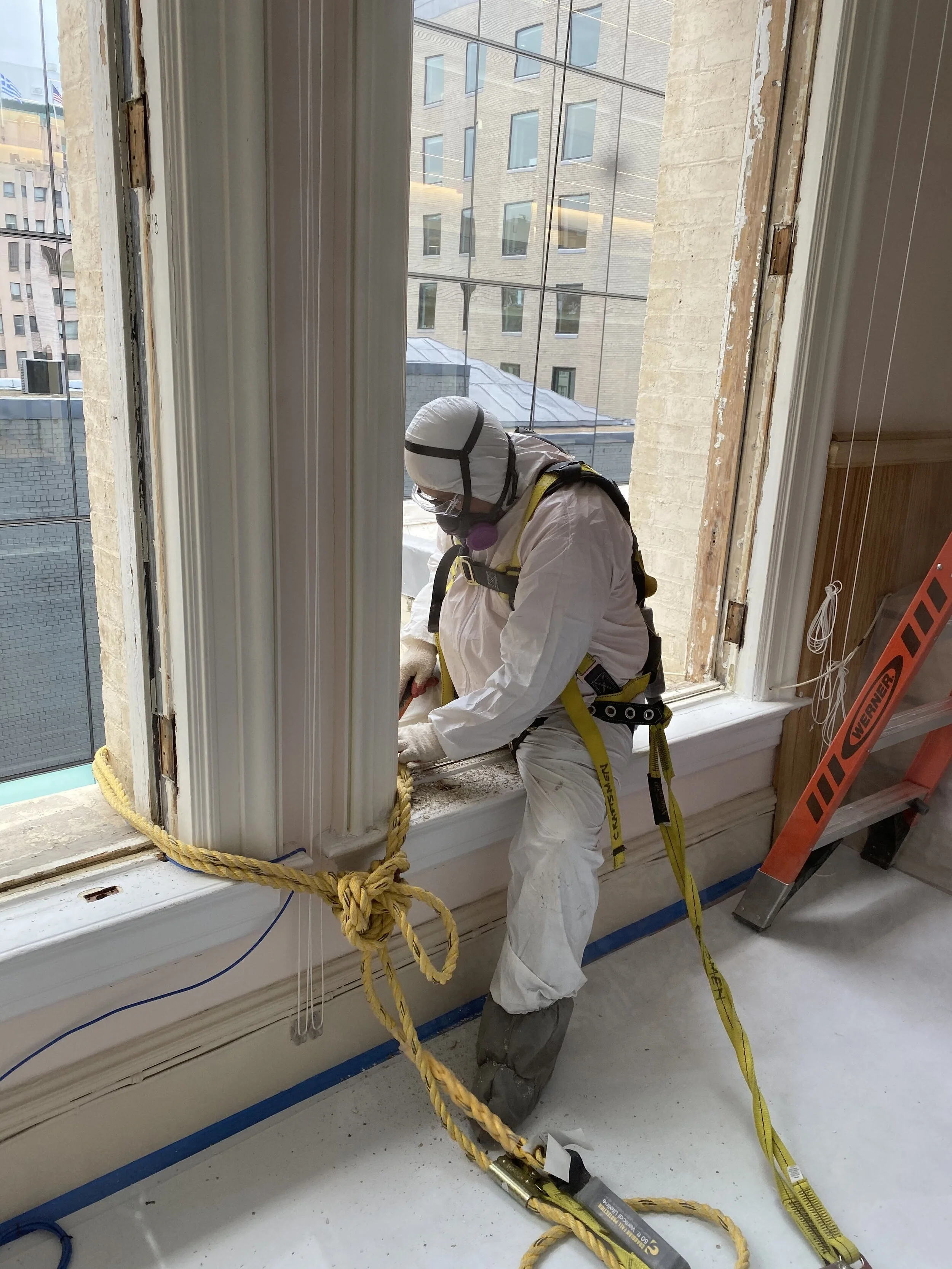
Our lead paint removal technicians have a keen sense for safety of themselves and the environment.
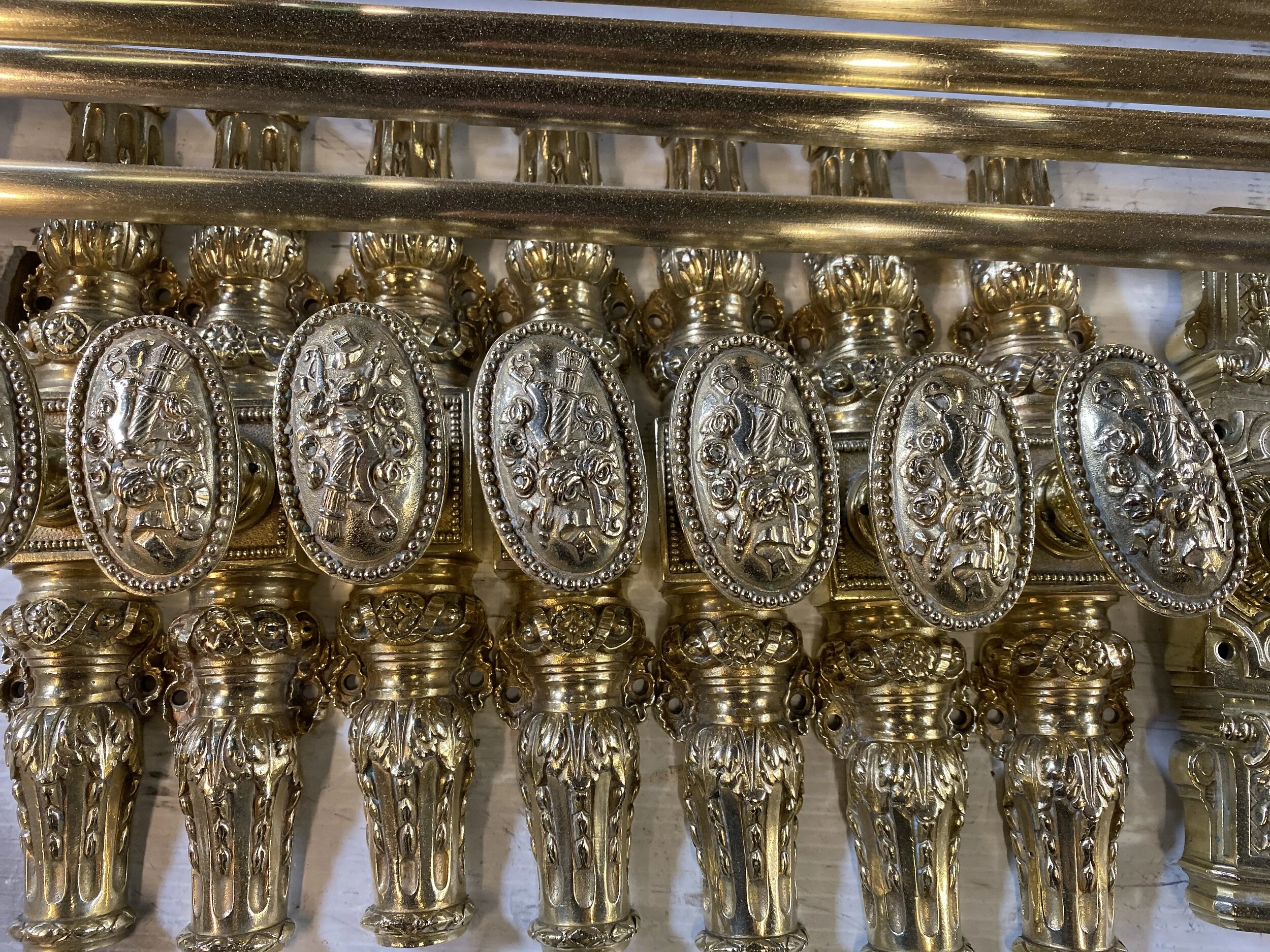
Details in this fine building are a bit more Czarist than Stallinist.

Stripping, cleaning, polishing, lacquering, and then lubrication before final assembly. Doing all this work in house gives us the control we need to finish a complicated project in a few months.

Cremone hardware is elemental to paired casement sash.
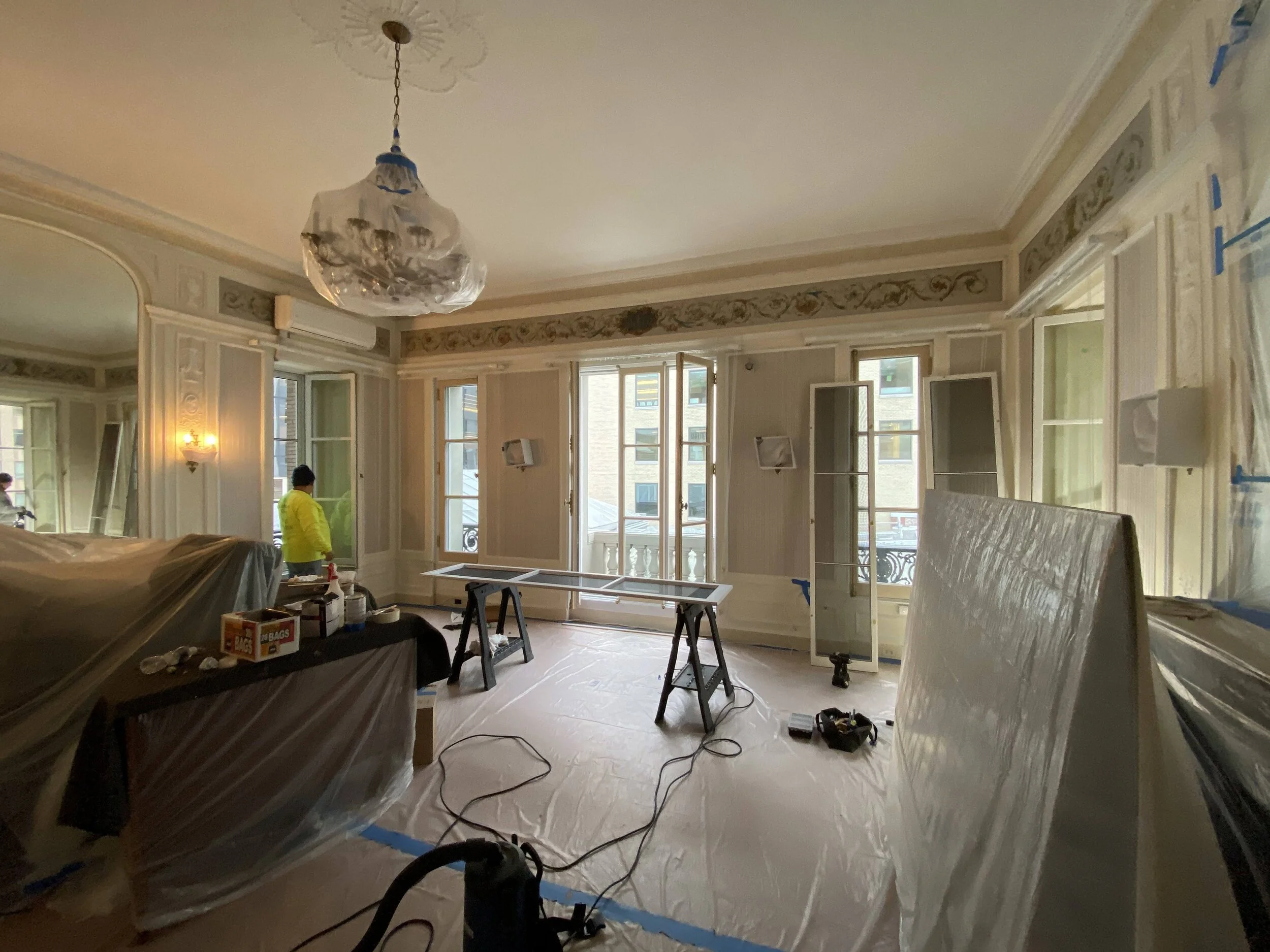
These window screens are solid Sapelle mahogany, as well, finished to the same level as the windows. They are readily removed for maintenance and will likely last 50 years.

The many profiles and surfaces involved in each sash and frame joint require precision fitment on site.
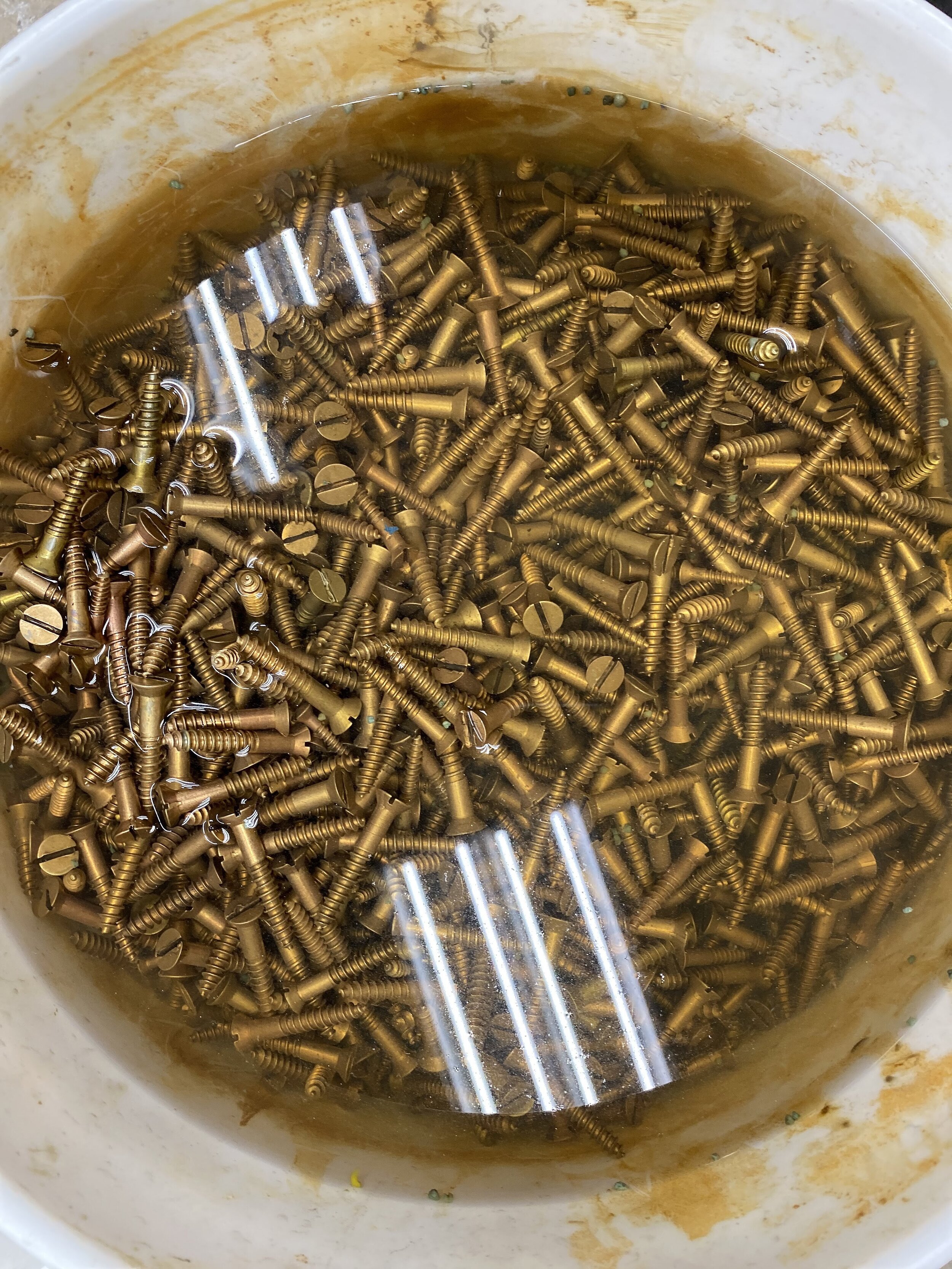
Yes, we restore the original slotted solid brass and bronze screws, as well.
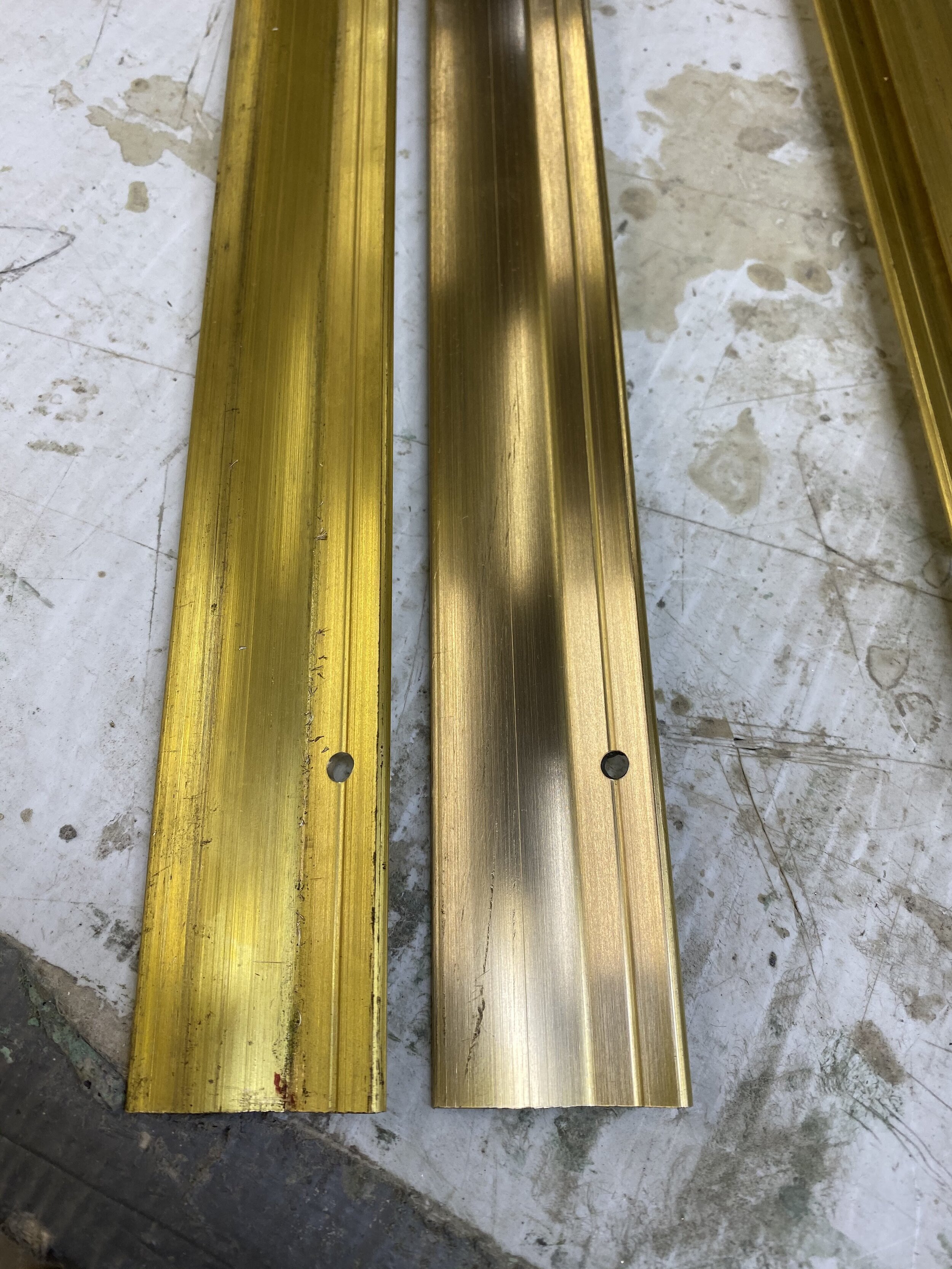
We used extruded bronze drip edges for durability, to the left is the original mill finish, to the right a piece satin burnished in our high energy tumbler.
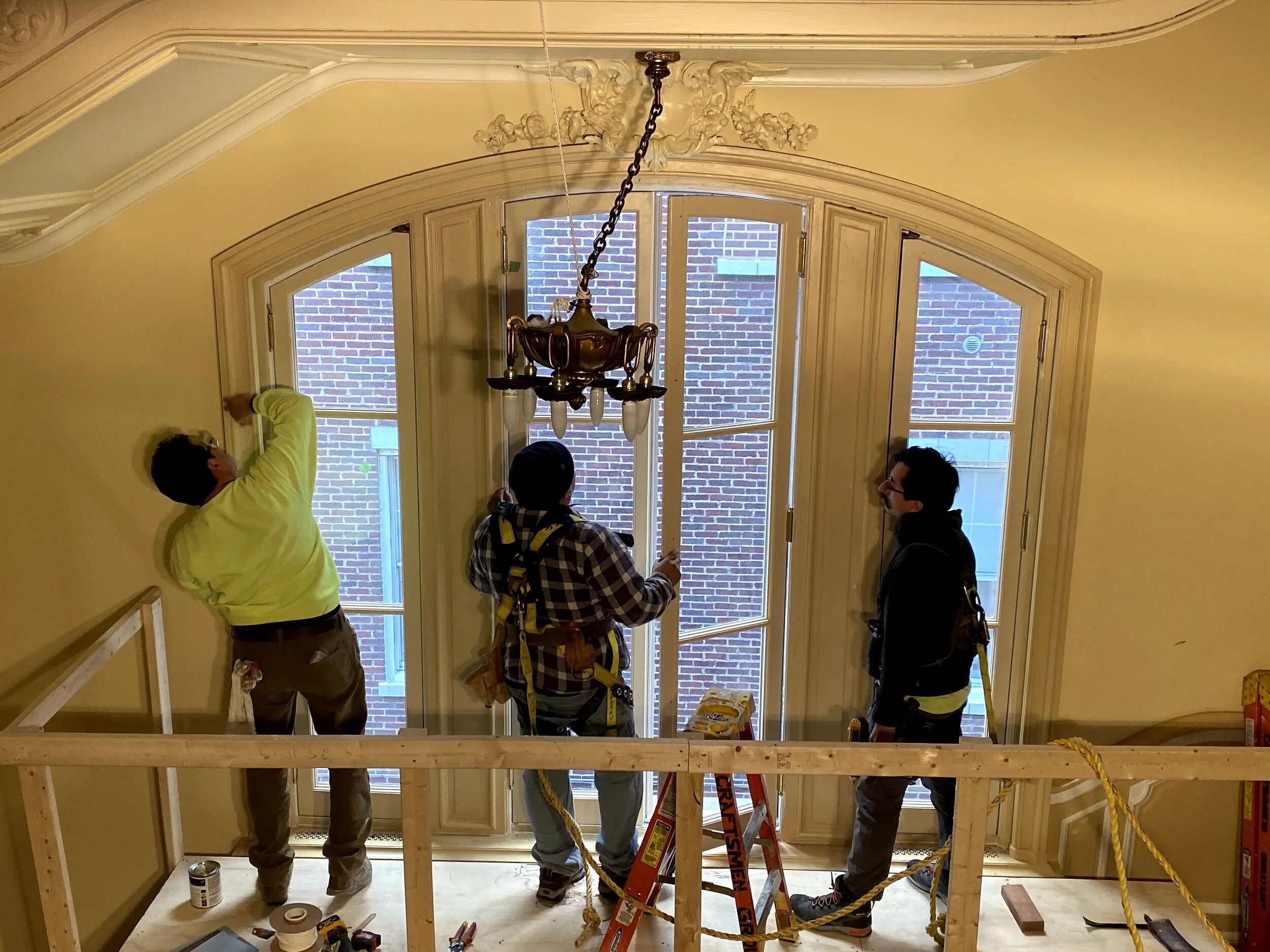
These radial sash require templating to achieve a precise fit.
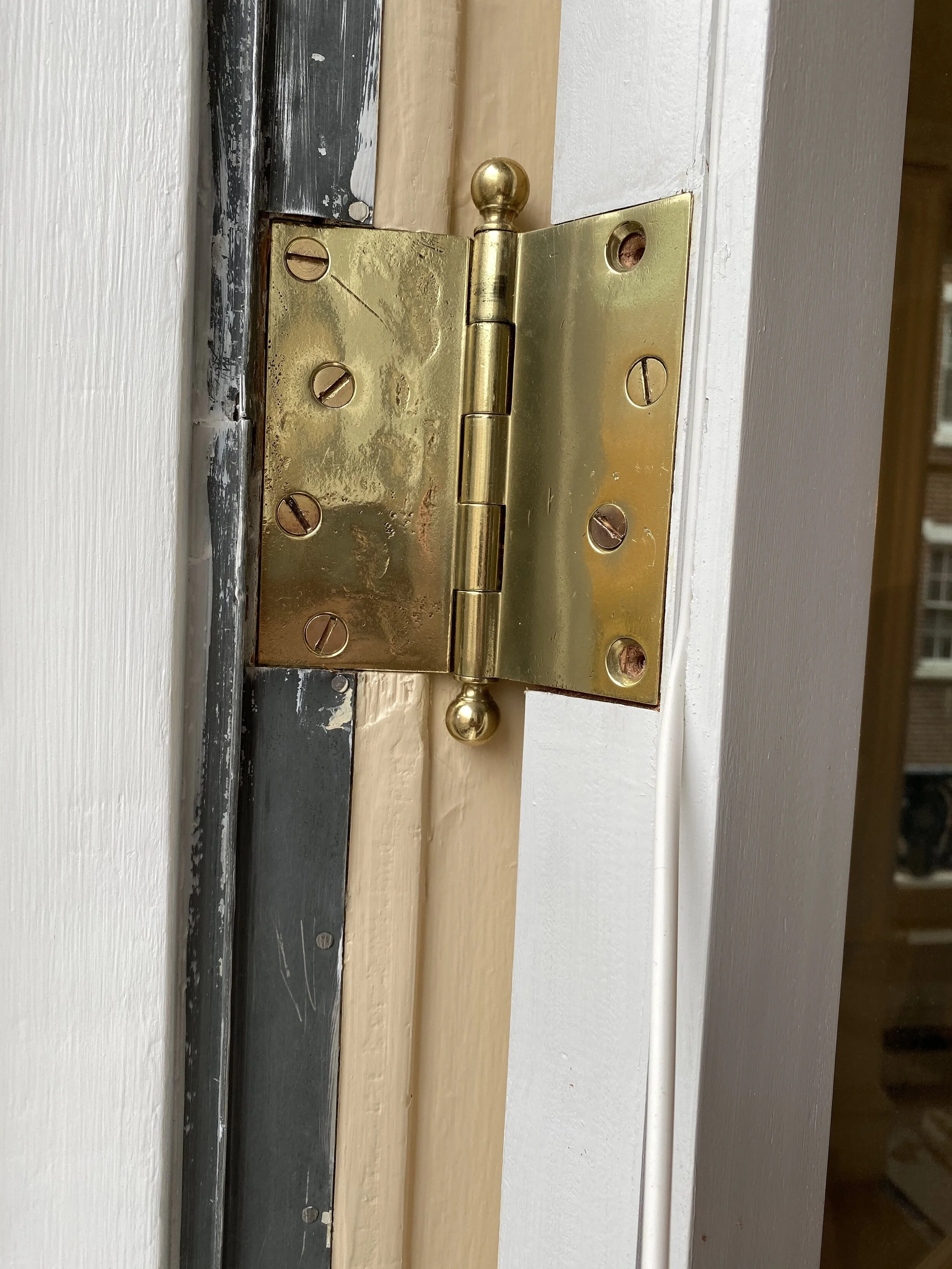
Note white rubber tube in groove adjacent hinge. This tube will be compressed against the 100 year old zinc weatherstripping at the frame. This discreet ingredient significantly improves the window’s attenuation of sound and thermal transference.
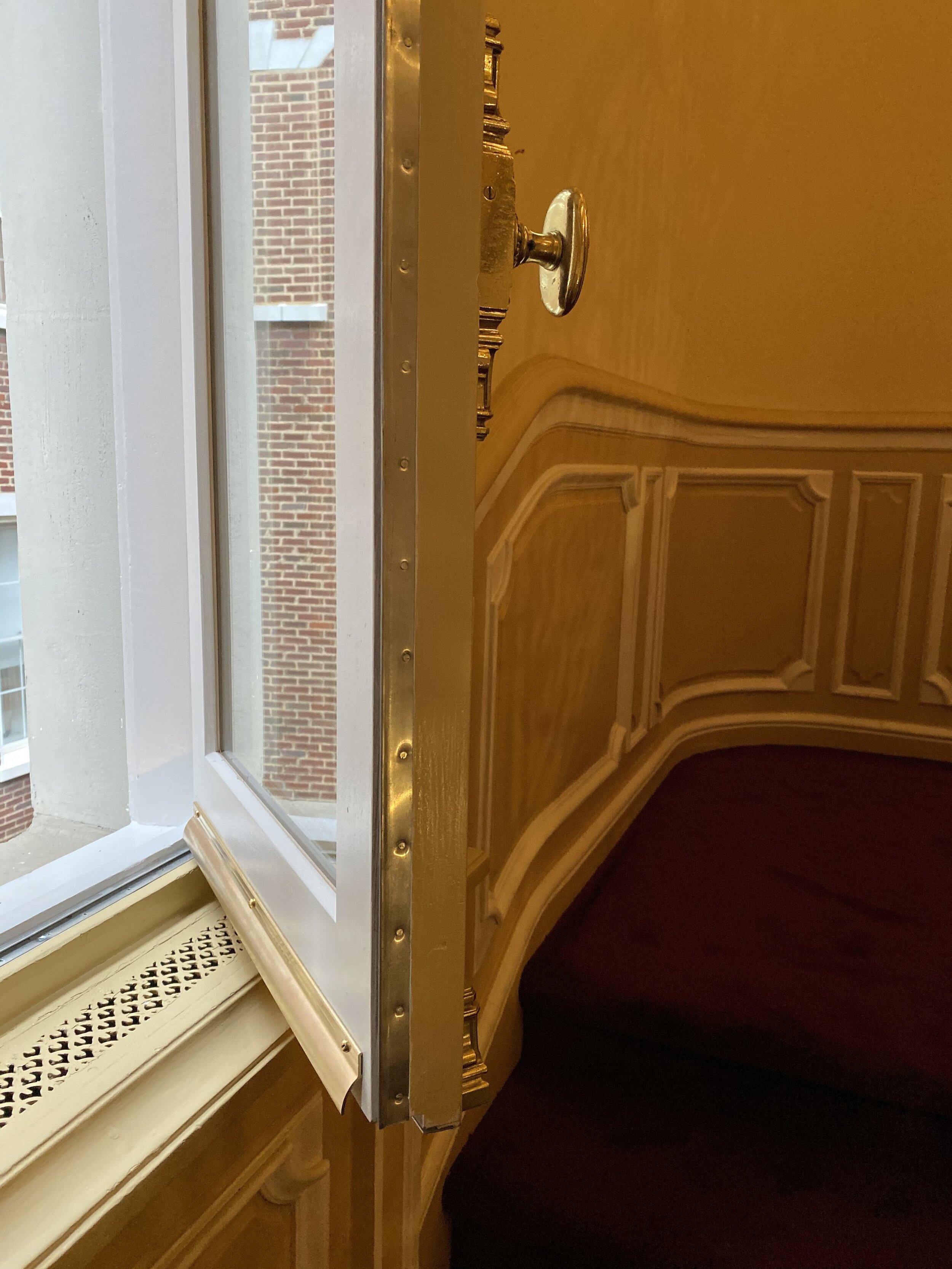
A completed casement with all its furniture.
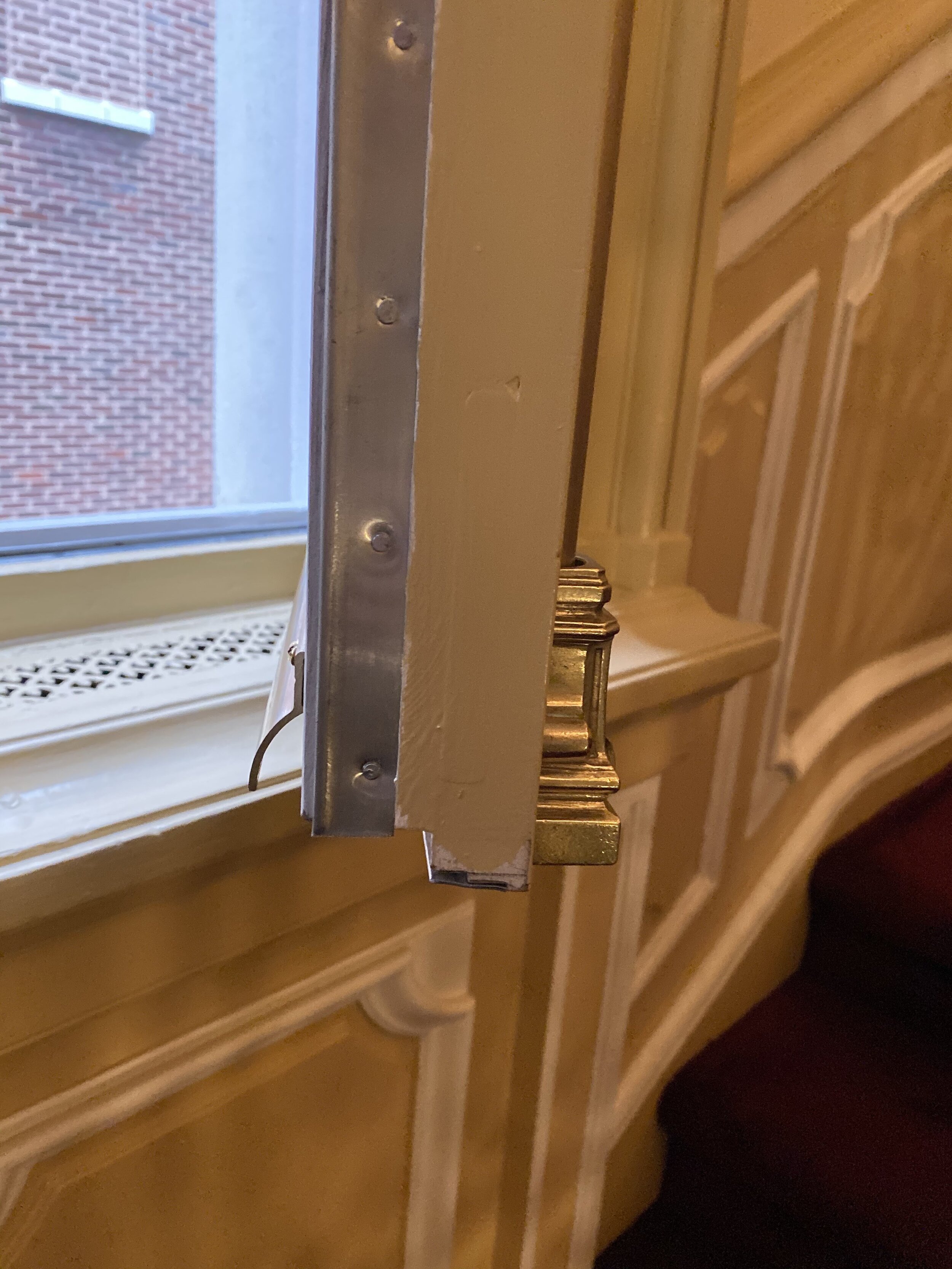

This window has an insect screen mounted outside. The muntin alignments took into consideration viewing at typical eye level so as here, one can barely see the screen.
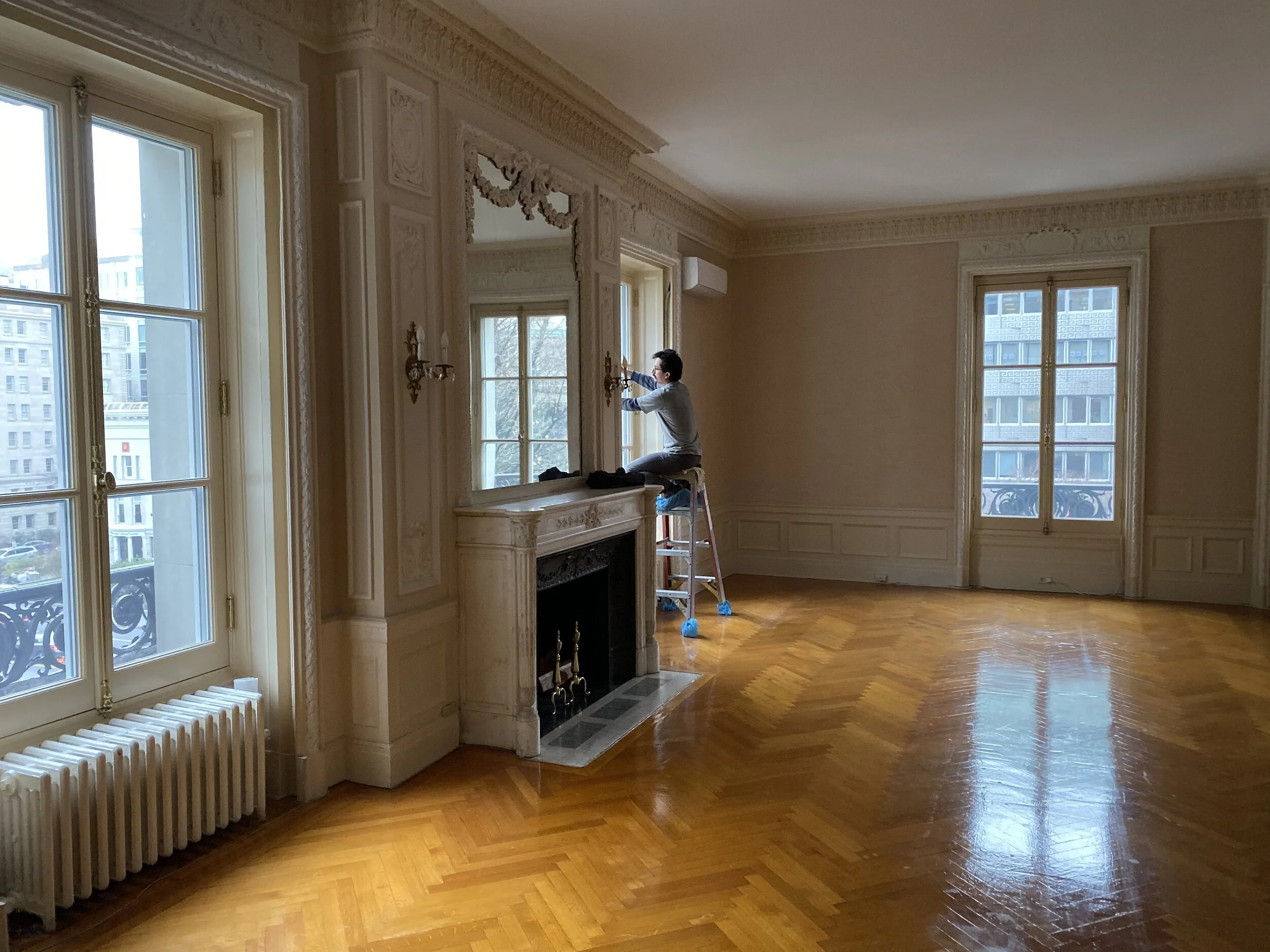
Meticulous final clean up, essential to a successful project.

Here you can see the window screens with original sash stays. New bronze drip edge is an original cremone keeper.
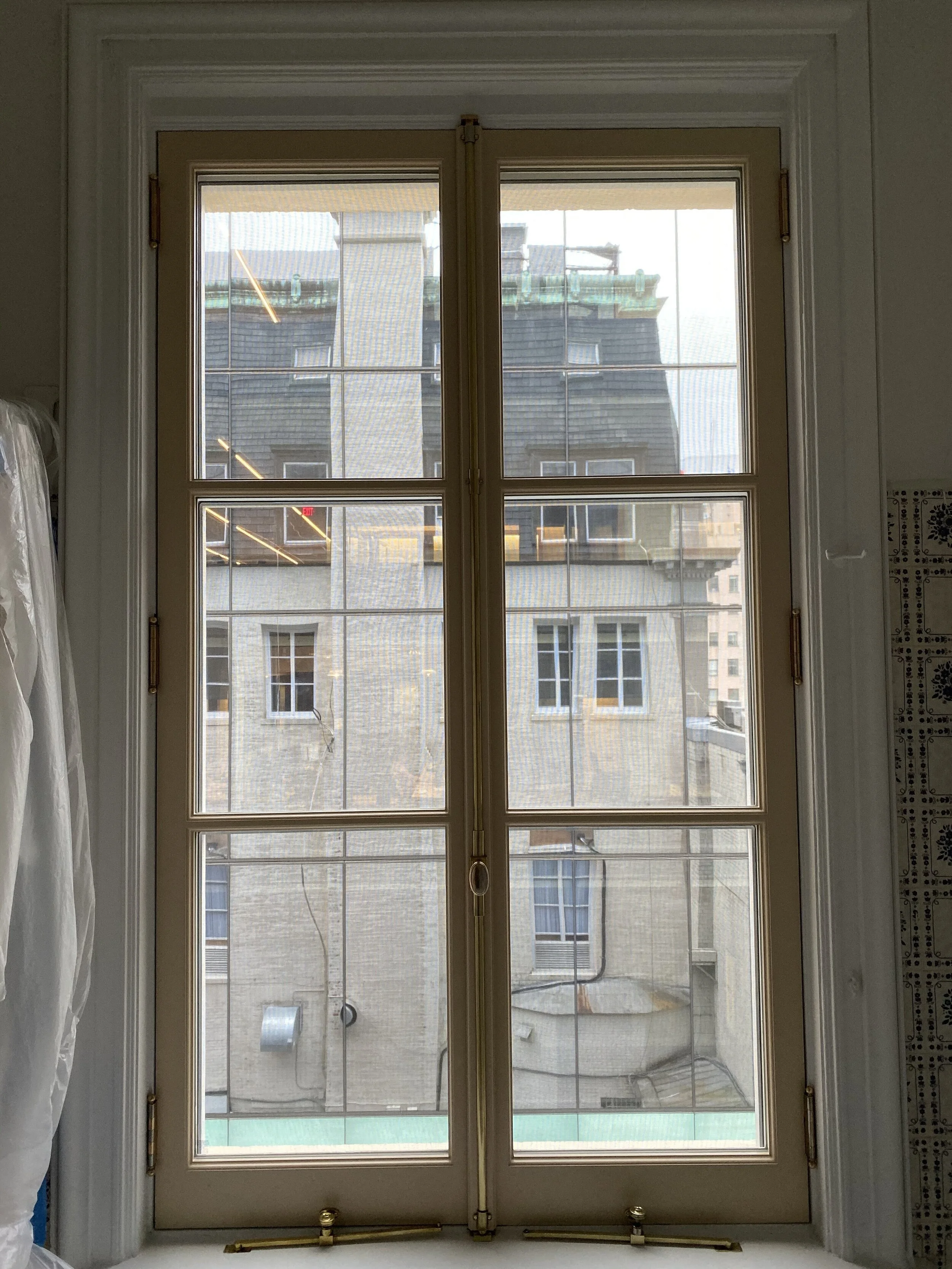
A wonderful phenomenon was apart of this building at its east elevation. A completely reflective modern structure returns back a view of the Russian residence. Windows at the center of this image are those that we reproduced.
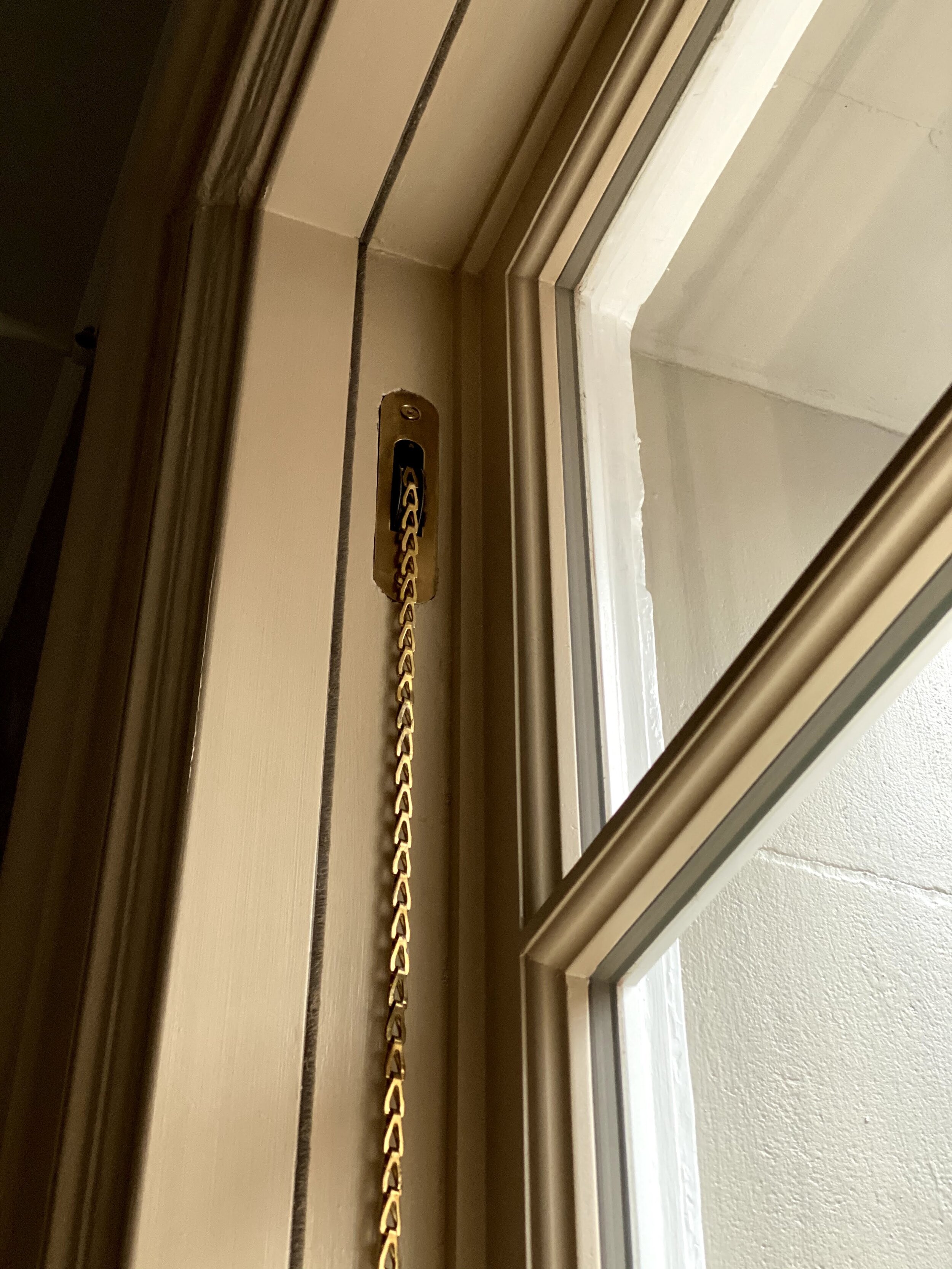
This shop is funny sometimes, here we restored the Russian pulley, but used the same chain installed at the Trump hotel.

Since the elevator, never again will steps be so elegantly made.